What is Additive Manufacturing? Everything You Need To Know
Additive manufacturing is an advanced manufacturing solution on the rise in many industrial applications. But do you know what exactly this technology is?
Additive manufacturing (AM) isn't just one process. It's a whole workflow that can impact product development from design to manufacturing. Let's dive into a look at how AM works, where it can be used, and what the future might bring.
How does additive manufacturing work?
Before we can understand how additive manufacturing works, we first have to understand what additive manufacturing is.
Additive manufacturing is a workflow that typically comprises several steps:
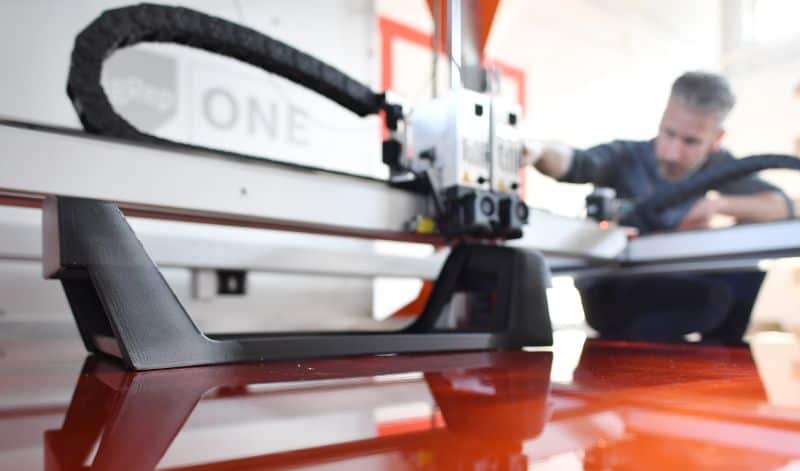
Each of these steps encompasses a workflow in and of itself, but these general steps lay out the basics. To fully consider AM, we have to think about three factors that will determine outcome: hardware, software, and materials.
The right selection in each of these areas is imperative to ensure success in an application -- and those choices often change between use cases, even within the same company. This may be as simple as selecting PLA material sometimes and PA6/66 other times, but adjusting the materials requires adjusting the software to program the 3D printer and tweak its printing parameters, and so on throughout every step of the process.
Essentially, a 3D CAD file is created with the design to be created. That file is then sent to a 3D printer for the actual print job. Once the print job is complete, the build is removed from the 3D printer and post-processing commences, including removing support material or smoothing the surface, as well as any other finishing work required (e.g., sintering, dyeing, assembling).
What's the difference between additive manufacturing and 3D printing?
While "additive manufacturing" and "3D printing" are often used interchangeably, these terms have different meanings. There are two ways to understand the difference:
Technically, 3D printing is one part of the additive manufacturing workflow, as laid out above. AM also involves the design and post-processing steps for end-to-end manufacturing.
Colloquially, "additive manufacturing" is used to refer to more industrial usage of these technologies.
Realistically, while there are differences between these terminologies, use of either is acceptable so long as whomever you're communicating with understands the reference.
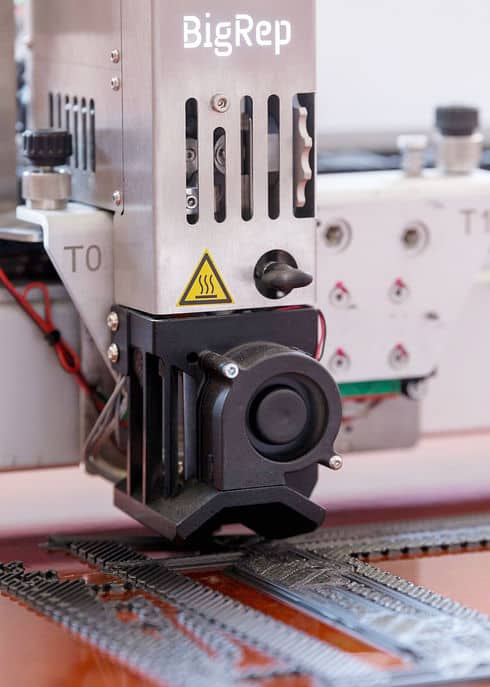
3D printing technologies
Several different processes fall under the umbrella of "3D printing". All are additive technologies that build up a part, often in a layer-by-layer process.
Standards body ASTM International officially recognizes seven additive manufacturing processes in the ISO/ASTM 52900 standard. Terry Wohlers lays these out as comprising:
- Material extrusion: an additive manufacturing process in which material is selectively dispensed through a nozzle or orifice
- Material jetting: an additive manufacturing process in which droplets of build material are selectively deposited
- Binder jetting: an additive manufacturing process in which a liquid bonding agent is selectively deposited to join powder materials
- Sheet lamination: an additive manufacturing process in which sheets of material are bonded to form a part
- Vat photopolymerization: an additive manufacturing process in which liquid photopolymer in a vat is selectively cured by light-activated polymerization
- Powder bed fusion: an additive manufacturing process in which thermal energy selectively fuses regions of a powder bed
- Directed energy deposition: an additive manufacturing process in which focused thermal energy is used to fuse materials by melting as they are being deposited
Most 3D printers available today, and virtually all that are commercially available and most commonly used, fall under one of these categories. Researchers are constantly developing new approaches, and the ASTM F42.91 Terminology Subcommittee reviews their categorization regularly to consider any potential additions whenever a new viable process emerges.
Additive manufacturing versus conventional manufacturing
Conventional manufacturing technologies include molding, CNC milling, welding, turning, forming, and many other well-known processes.
The easiest way of understanding the difference between traditional subtractive and additive manufacturing processes is quite simple: they are effectively opposites. Subtractive processes like CNC milling begin with a block of material and remove material until the desired geometry is attained. On the contrary, in additive manufacturing, material is built up and added to create that geometry.
AM is capable of producing more complex internal structures than had previously been possible. While, for example, traditional technologies must create complex objects in multiple parts to be later assembled, 3D printers can create complex objects as a single piece.
Application areas inform the decision to use additive, subtractive, or a hybrid approach of both manufacturing technology types. For example, additive manufacturing is well-suited for producing high-value, low-volume parts. Conventional techniques like injection molding, on the other hand, are more feasible in low-value, high-volume production.
Design for Additive Manufacturing
Different design considerations come into play for 3D printing than when designing for conventional technologies. Design for additive manufacturing (DfAM) takes into account the need to build a part up, rather than subtract material or create a mold.
Simply translating an existing part's design file into a 3D printable format will not guarantee printability. Even if it does, that part as it is may still be better made traditionally, as it has not been optimized for 3D printing. Optimizing a design for 3D printing is a much more efficient path to best leveraging all the benefits AM has to offer.
Existing software has in many cases been updated to allow for DfAM-specific approaches. These updates are necessary, for example to ensure that 3D models are watertight. Other considerations include the creation of supports, orientation on the build plate, and overall printability.
New software offerings have also appeared, dedicated from the beginning to DfAM.
DfAM approaches increasingly include new artificial intelligence (AI)- and augmented reality (AR)-geared software. This may include parametric modeling, topology optimization, and/or generative design. Through such design approaches, software can automatically ensure that input parameters are met.
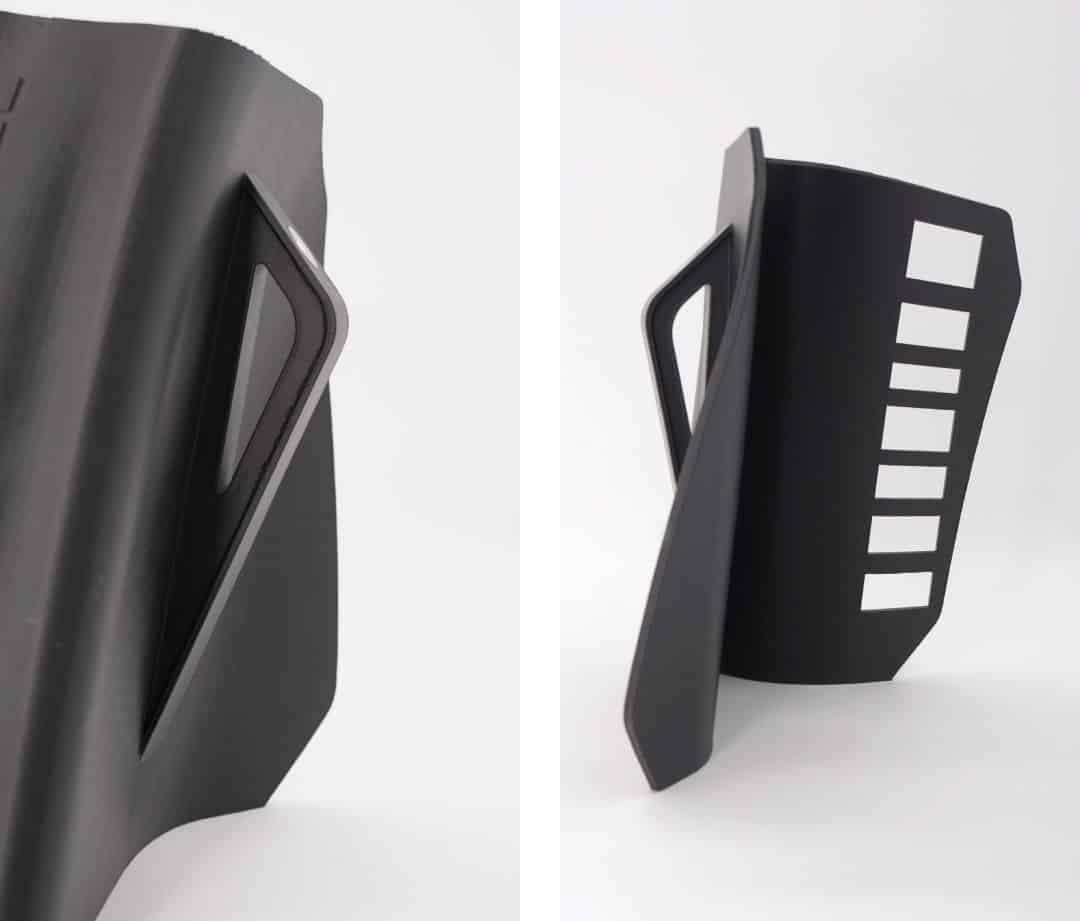
Design for Additive Manufacturing
Different design considerations come into play for 3D printing than when designing for conventional technologies. Design for additive manufacturing (DfAM) takes into account the need to build a part up, rather than subtract material or create a mold.
Simply translating an existing part's design file into a 3D printable format will not guarantee printability. Even if it does, that part as it is may still be better made traditionally, as it has not been optimized for 3D printing. Optimizing a design for 3D printing is a much more efficient path to best leveraging all the benefits AM has to offer.
Existing software has in many cases been updated to allow for DfAM-specific approaches. These updates are necessary, for example to ensure that 3D models are watertight. Other considerations include the creation of supports, orientation on the build plate, and overall printability.
New software offerings have also appeared, dedicated from the beginning to DfAM.
DfAM approaches increasingly include new artificial intelligence (AI)- and augmented reality (AR)-geared software. This may include parametric modeling, topology optimization, and/or generative design. Through such design approaches, software can automatically ensure that input parameters are met.
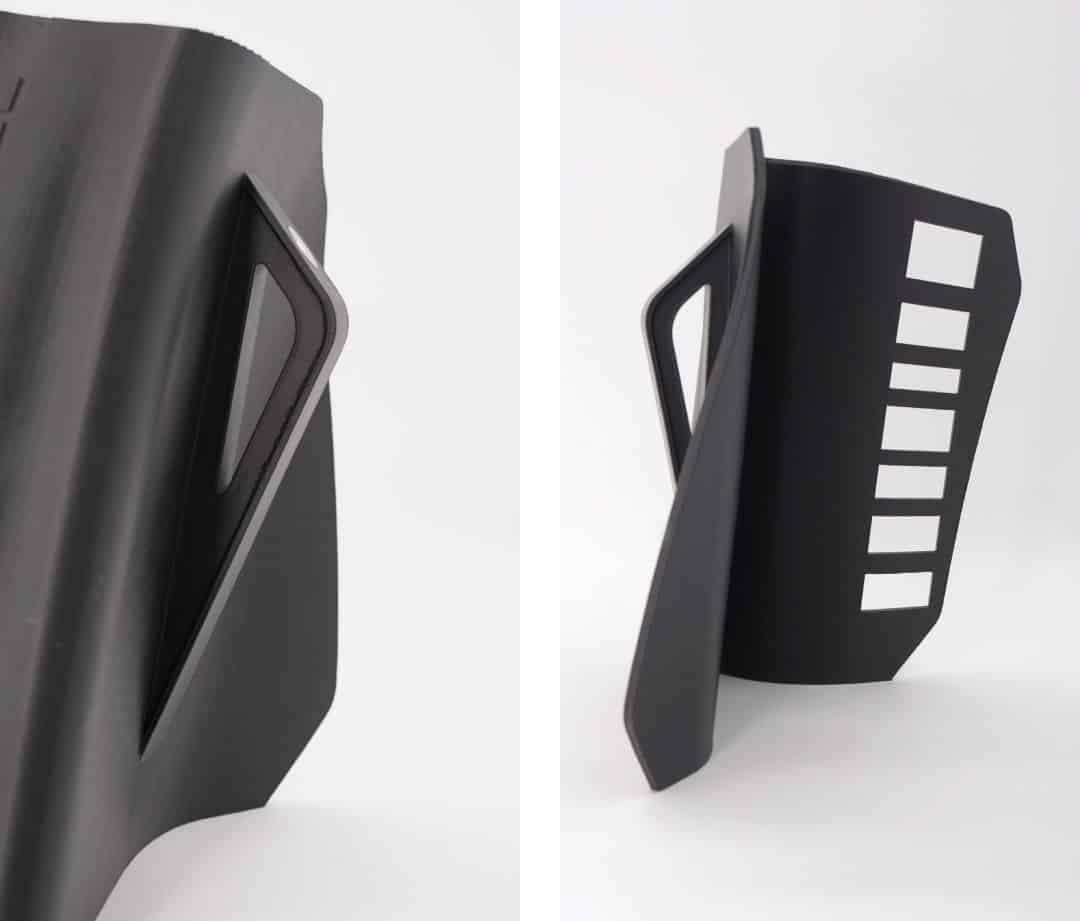
Additive manufacturing in different industries
Additive manufacturing is seeing increased adoption globally across a growing number of industries.
Automotive
Beginning with prototyping, major automotive suppliers have been working with 3D printing technologies for decades. Both metal and polymer technologies come into play as automotive original equipment manufacturers (OEMs) 3D print prototypes, jigs and fixtures, tooling, and end-use parts.
Aerospace
Aerospace is singularly well-suited for AM and 3D printing due to some key benefits of the technology. These include the ability to reduce part counts, lightweight existing designs, create more complex internal structures, and optimize performance. Metal 3D printing in particular is on the rise for end-use part production in the aerospace industry.
Consumer Goods
Prototyping, finished products, and spare parts are all increasingly 3D printed in the consumer goods sector. From toys and games to small appliances, if it finds its way into the hands of consumers, chances are there's a place for additive manufacturing in production workflows.
Research and Education
The term "3D printing" first emerged from MIT in the 1980s. This technology has its very roots in research and education. Researchers often experiment with new processes, unique materials, and cutting-edge application areas from the nanoscale to outer space structures. Educational institutions lead many R&D initiatives, though students as young as kindergarten age are now also finding 3D printers in their classrooms.
Contract Manufacturing
Industrial use of additive manufacturing is on the rise as well in contract manufacturing operations. Service providers offer immediate access to industrial 3D printers and the expertise to operate them. These operations can be of great value when additive manufacturing is only occasionally required, or when use of higher-value systems or materials is needed. Contract manufacturers often also offer complementary technologies including CNC mills and other conventional manufacturing equipment.
Construction
3D printing with extruded cement or custom-made formwork can quicken the construction process of building structures. New shapes of dwellings can be made on massive structural 3D printers. Buildings, bridges, and other structures are able to be 3D printed in cement, plastic, metal, and even dirt. 3D printed forms for concrete pouring offer another way to bring advanced manufacturing capabilities into a more conventional construction workflow.
Applications for Additive Manufacturing
3D printing initially emerged as a prototyping technology. As processes have matured and materials science has accelerated, additive manufacturing is now used throughout the full production cycle.
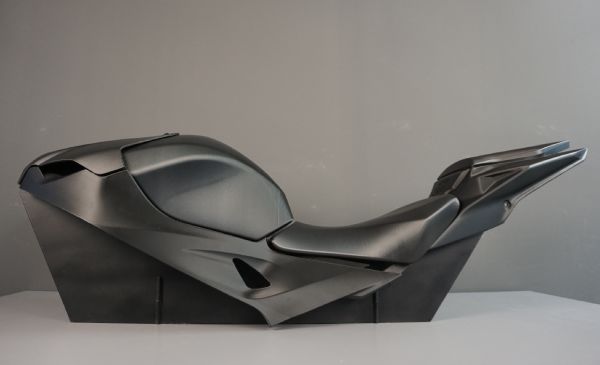
Product Development with Rapid Prototyping
3D printing was so synonymous with rapid prototyping, that "RP" was one of the first common terms for the technology in manufacturing operations. An experienced team can redesign and 3D print a next iteration as quickly as same-day. This cuts dramatically down from previously normal lead times of weeks or even months between conventionally-made prototypes.
Iterations from proof-of-concept through to functional prototype can all be 3D printed. This brings the cost and time savings across the entire product design cycle. Rapid prototyping can also increasingly be done using the same 3D printing technology as will be used for the final product.
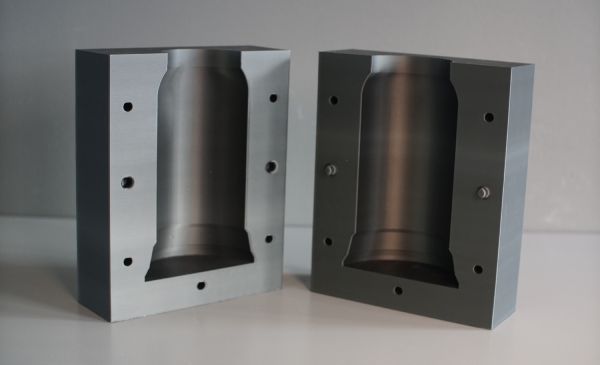
Rapid Tooling
Tooling, jigs, fixtures, and other traditional manufacturing accessories can be quickly and easily 3D printed. In-house 3D printing can dramatically speed up the process of making customized tooling for any manufacturing job. Faster, less expensive tooling production can lead to faster, less expensive overall production.
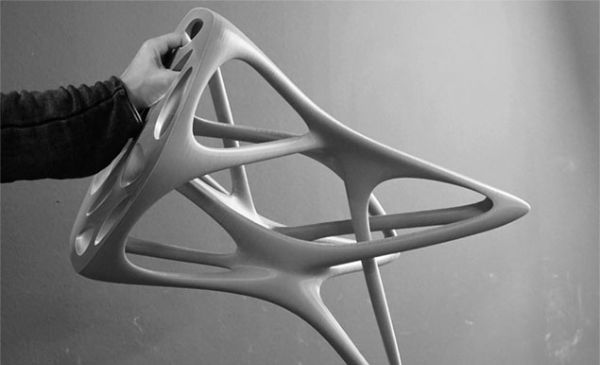
Rapid Manufacturing and Mass Customization
Manufacturing cycles can be dramatically sped up with additive manufacturing. Removing the need for tooling, lowering labor time and costs, and localizing production offer a more rapid manufacturing process.
Because a 3D printer can treat every design file on its build platform individually, mass customization is also possible. With mass customization, each part can be made slightly differently, for example to fit a size or shape need. This comes in handy especially in creating items like insoles, orthodontic aligners, or hearing aids that best serve their purposes when custom-fit to the wearer.
Additive manufacturing advantages
Additive manufacturing has many advantages over traditional manufacturing processes. While they cannot be viewed in a vacuum, these advantages can lead to significant improvements in workflow and final product.
When appropriately utilizing DfAM, freedom of design can be unlocked. Holes that conventionally needed to be made perfectly round can now be any shape. Internal structures can be as complex as needed without necessitating multiple parts that would have to be assembled. Complex geometries, such as optimized lattices, can offer not only new shapes but enhanced performance. Multi-material 3D printers also enable different colors or material properties within a single build. Topology optimization and biomimicry often go hand-in-hand to offer unique designs offering minimal material use and high tensile strength.
Products can be made in completely new ways, in completely new designs. Removing constraints of design and manufacturing allows for optimal production workflows to emerge.
Rapid prototyping, localized production, and new design cycles can dramatically boost the time-to-market for new products. Removing not only the need for tooling but the need for offshoring, additive manufacturing enhances speed to market. With each step of the product development cycle streamlined, the overall production timeline can be made more efficient.
With decentralized production capabilities, additive manufacturing shortens and secures the supply chain. Offshore production can lead to instability in logistics, such as in times of global pandemic, for example. Localizing production means that a digital design file can be created in one place and sent anywhere with the appropriate 3D printing installation for production. Advances in software are ensuring the intellectual property (IP) security of proprietary designs as well.
The Future of Additive Manufacturing
Additive manufacturing currently accounts for a relatively small portion of the approximately $12 trillion global manufacturing industry. Each year, though, that portion is expanding. Annual growth in spending on 3D printing hardware, software, and materials is often in the double-digits.
As additive manufacturing continues to mature as a part of the overall manufacturing industry, so too does it mature as a technology suite. More materials, such as high-temperature, medical-grade, and familiar metals and polymers, are becoming available. Software integrations are allowing for real-time in-situ 3D printing monitoring, reducing the occurrence of failed print jobs. 3D printers themselves are becoming capable of ever-improved qualities in terms of accuracy and reliability.
Forces driving the future of additive manufacturing include investment and training. Investment into AM operations remains on the rise. Access to funds enhances companies' capabilities to work toward next-generation improvements and technology improvements. Training, from grade school through career-track upskilling, is formalizing at all levels. Focus on awareness of and training in such skills as DfAM and additive manufacturing workflow will see more companies' workforces equipped with the next generation of production technologies.
FAQ: Get your questions answered quickly
Additive manufacturing, or 3D printing, is a manufacturing process in which thin layers of material are applied layer by layer to create a three-dimensional object. It is called additive manufacturing because the material is gradually added to the resulting part.
Additive manufacturing thus contrasts with traditional manufacturing processes, in which material is removed from a piece of material to create the desired geometry.
The most commonly used materials for additive manufacturing are plastics in filament or powder form. However, 3D printing of carbon fibers and metals is also becoming more common. Additive manufacturing can produce components with very complex shapes and without the need for additional tooling.
Learn More in Our Additive Manufacturing Use Cases
Find Your Industrial Additive Manufacturing Machine
A truly industrial 3D printing experience
A large-format 3D printer designed for high productivity in industrial manufacturing environments. It's an additive manufacturing system with the speed and reliability to supercharge your production with high-quality industrial parts.
Find your industrial Additive Manufacturing solution
A truly industrial 3D printing experience
A large-format 3D printer designed for high productivity in industrial manufacturing environments. It's an additive manufacturing system with the speed and reliability to supercharge your production with high-quality industrial parts.